Comparing Rotational and Injection Molding | RPP Containers
June 7, 2021
Rotational Molding vs Injection Molding
At RPP containers, we strive to provide the best in bulk. That is why a large majority of our containers are made by injection molding. However, before we get into that, let us go over what those are and the pros and cons of both.
What is rotational molding?
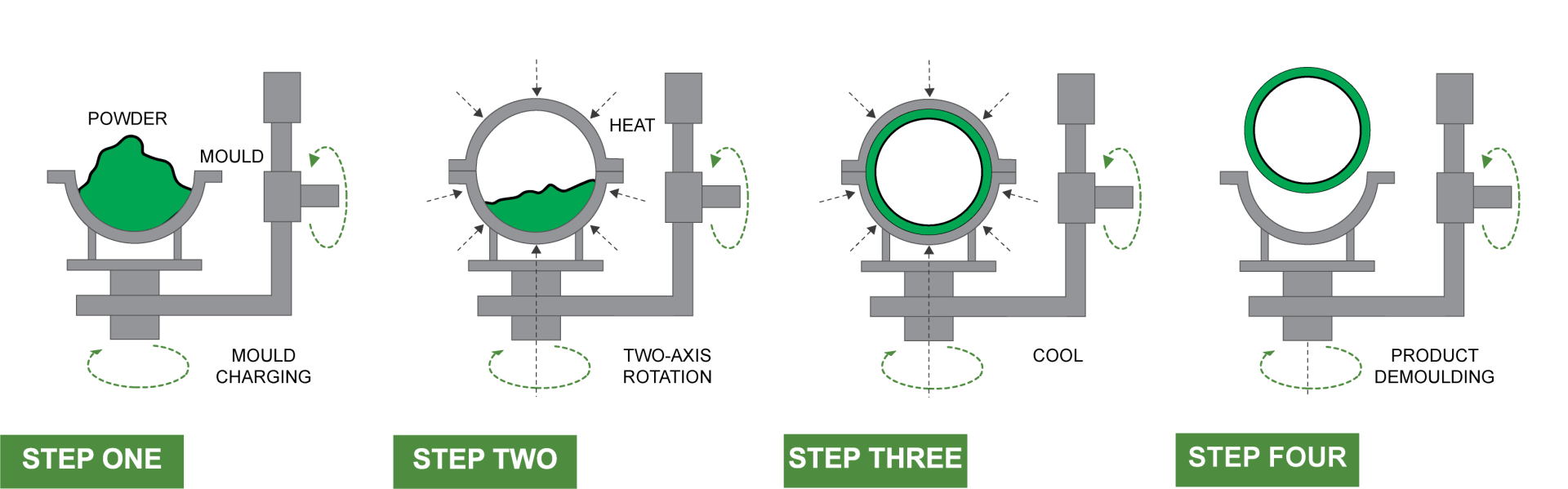
Rotational molding happens when plastic powder or liquid resin is added to a hollow mold and rotated bi-axially in an oven (similar to the process for a rotisserie chicken) until it melts and coats the inside of the mold cavity. Then, you must wait for the tool to cool and the plastic to solidify. Lastly, remove the plastic part from the tool and you have your part.
The advantage of this method is that the molds are much lower costs, affording greater variation or customizability in your products. Additionally, it takes much less time to develop a mold for rotational molding, shortening lead times on new products. However, if you are mass-producing a product or need it to have intricate designs, rotational molding may not be the best method. This method is used for things like canoes, yard flamingos, road cones, footballs, and planters.
What is injection molding?
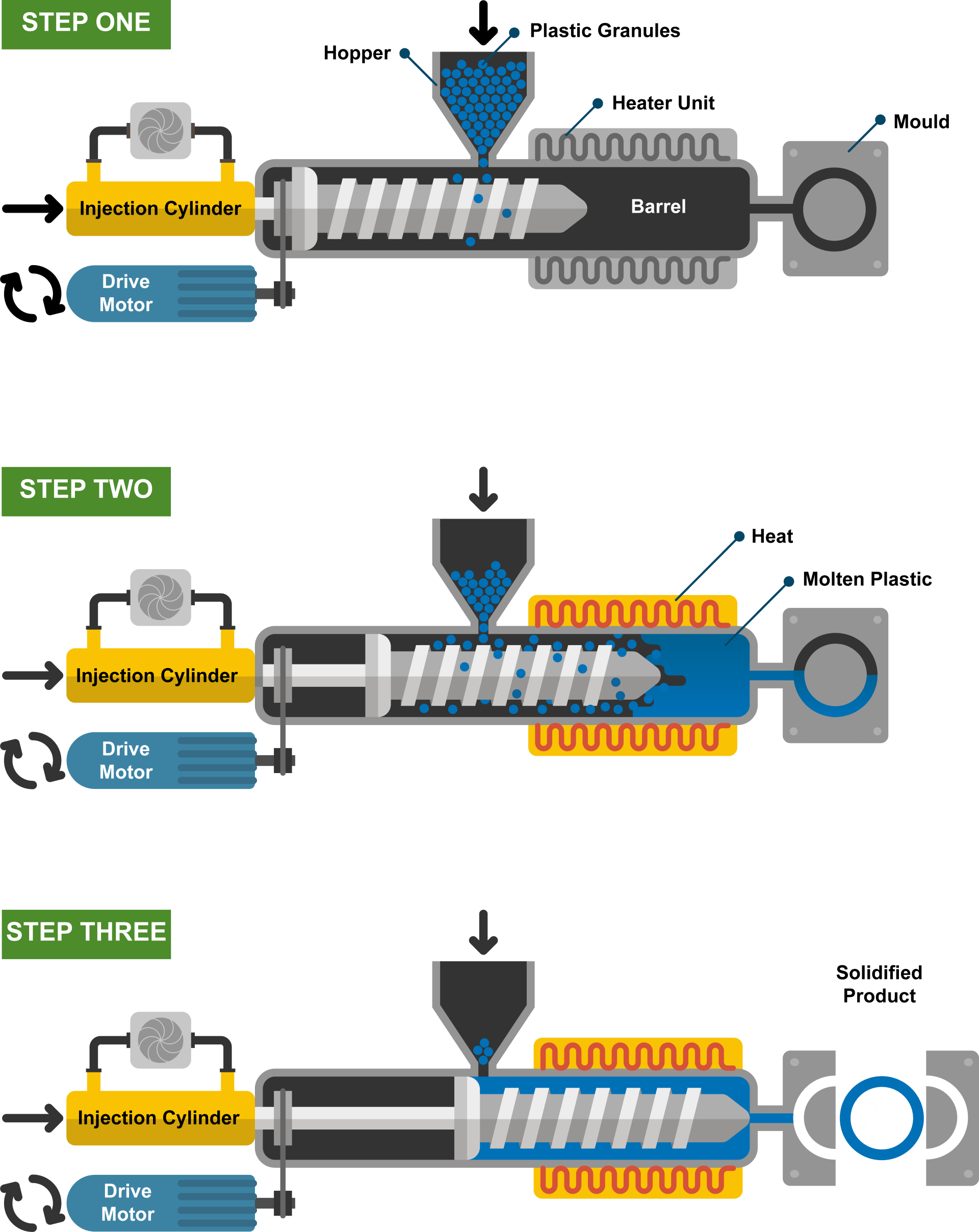
Injection molding occurs when a tightly held mold is injected with a melted plastic mixture in. The plastic is already hot when injected, and you must wait for it to cool down once it is injected into the mold. The molds for injection molding take a long time to produce, and it is a costly process. There is typically a lot of thought that goes into the design because there is usually more time and money invested into these.
Many or our containers have complex designs. This is because engineers are behind the scenes figuring out how to optimize durability while minimizing the plastic used to create longer lasting, stronger, and more inexpensive containers. Once the mold has been created, injection molding is far more efficient mass-producing products. We can deliver a larger number of products in less time and also save on labor costs. We chose to optimize costs and give you the best in
bulk containers
.
For a lot of our containers, we use a process called structural foam injection molding. This is a variant of injection molding where gas is added during the injection process, increasing aeration in the plastic. It has rigid skin and a more cellular structure. It lowers the weight of the parts and reduces stress on the plastics. These are great to use with forklifts as they are much less likely to snap from blunt force. These are the containers that do not have that sheen plastic look to them.
If you do not see a container that is exactly to your liking, we also offer customizable options. See more about there here
/news-events/customized-to-meet-your-needs
.
If you have any questions about how our containers are made feel free to give our sales representatives a call at (513) 489-2244, visit our
contact page
,
or use our chat feature on our website.
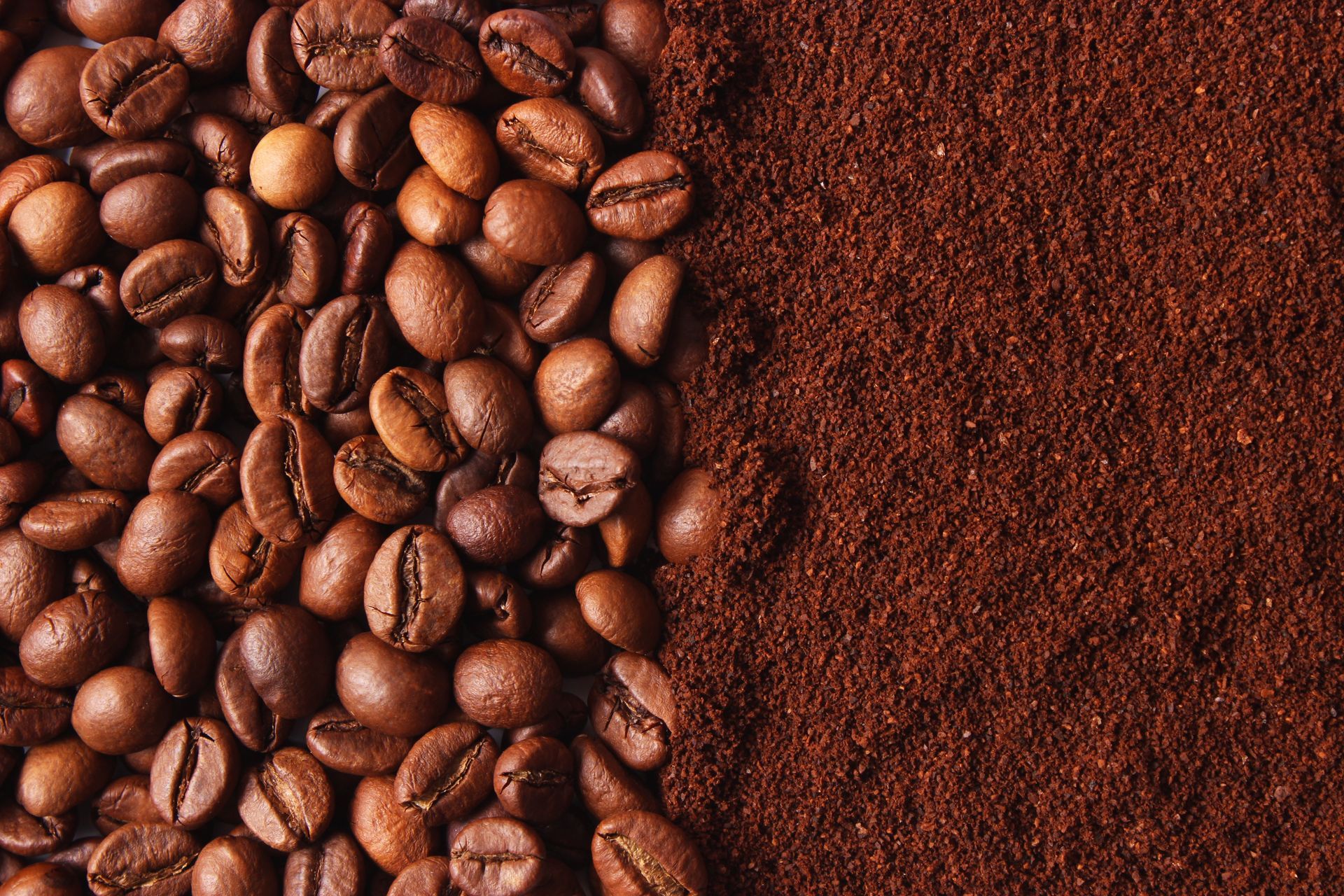
When it comes to preserving the freshness and quality of your coffee beans, every detail matters—especially the storage containers you choose. In the world of coffee production, maintaining the integrity of the beans from roasting to final delivery is essential. That's where RPP Containers steps in with their reliable plastic hopper bottom containers, a game-changer for anyone involved in the coffee business, from roasters to retailers.
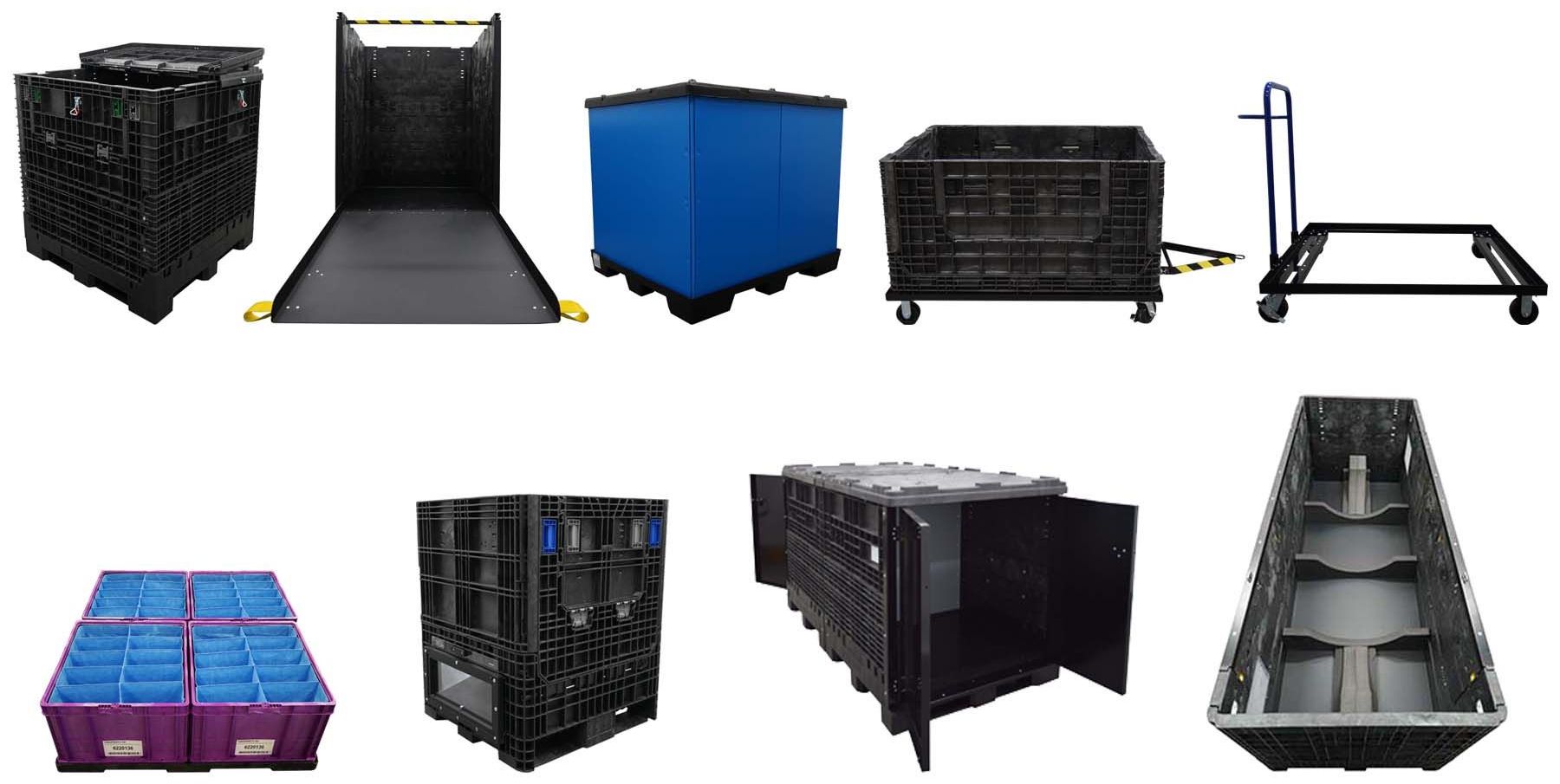
In the world of material handling and logistics, one size does not fit all. That's where RPP Containers steps in with its innovative CustomBulk solutions, designed to address the unique challenges businesses across various industries face. Whether you're dealing with oversized components or sensitive materials or need something beyond the standard container offerings, CustomBulk by RPP Containers is your go-to for tailored, practical solutions.
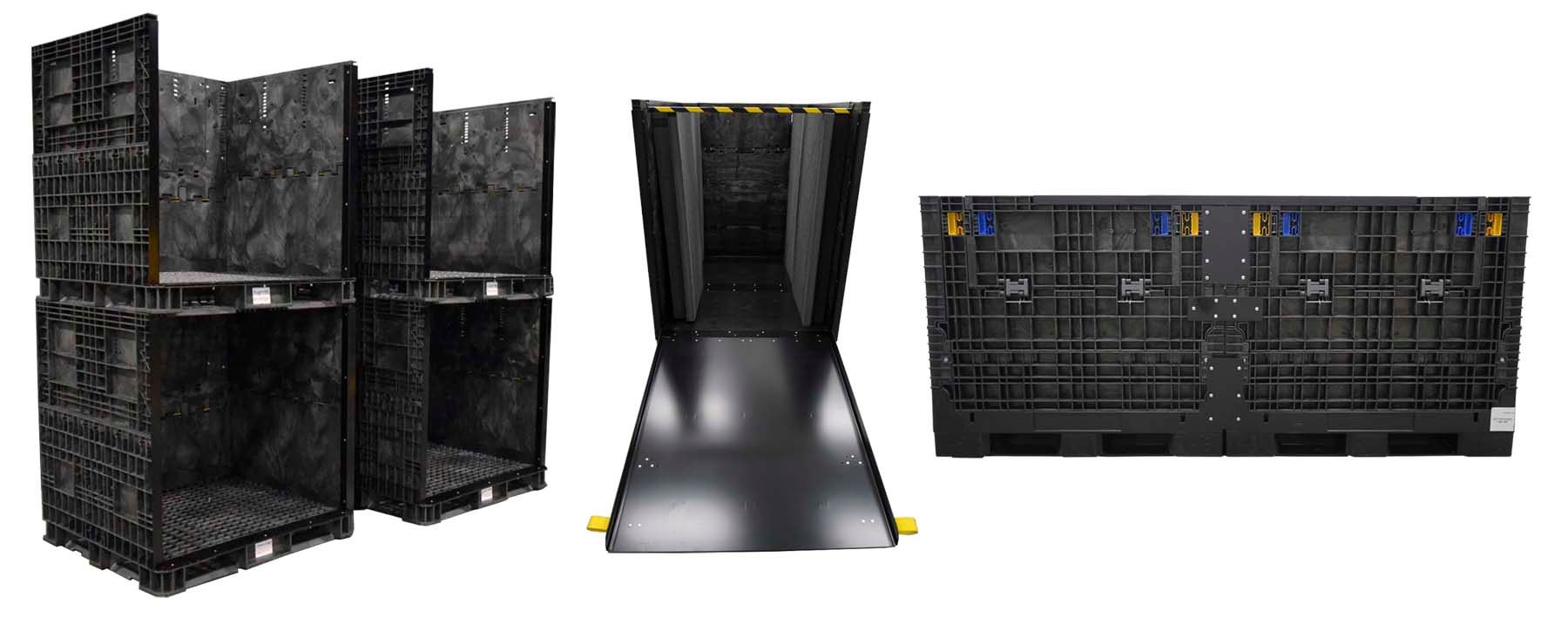
In the ever-evolving world of industrial storage, reliable, efficient, customizable bulk containers are paramount. Companies across various sectors—from manufacturing to logistics—require storage solutions that meet their unique specifications and enhance operational efficiency. This is where RPP Containers steps in with its innovative custom bulk containers designed to address these precise needs.
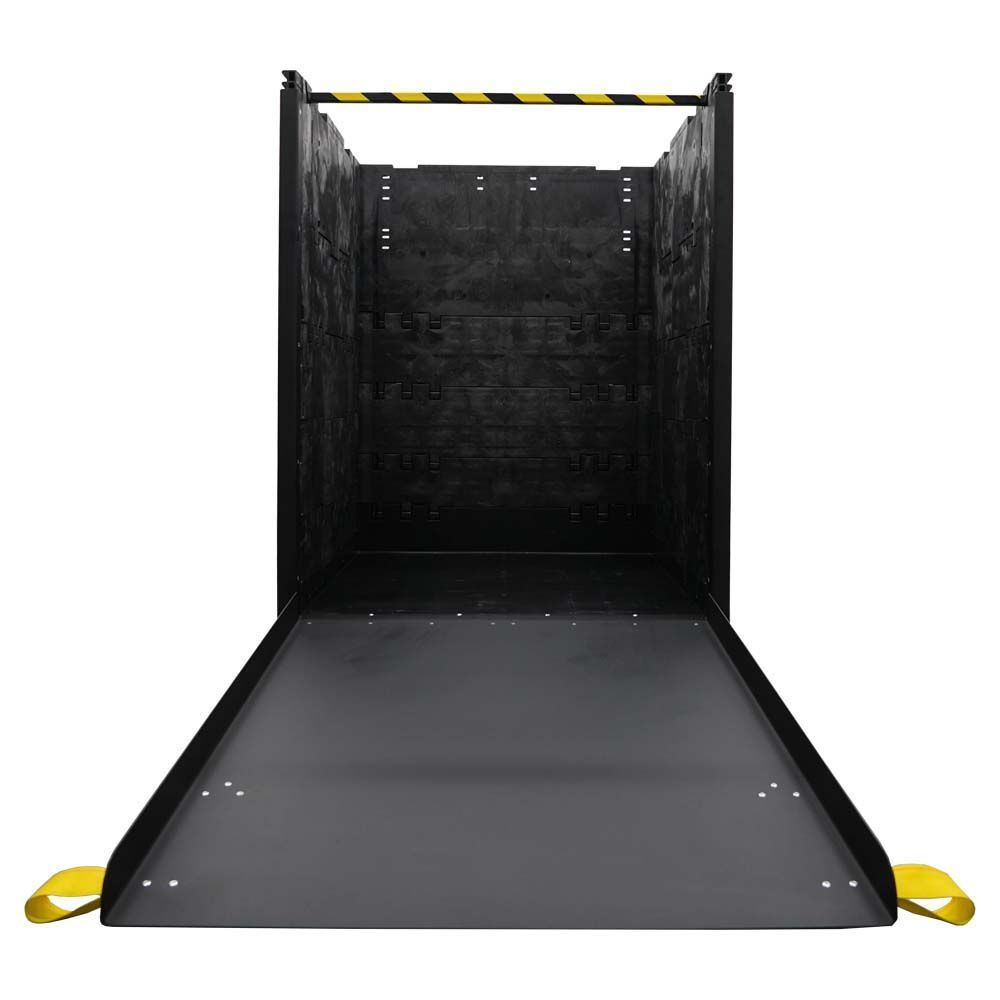
In the world of industrial storage and transportation, efficiency and durability are paramount. As businesses strive to optimize their operations, the demand for innovative storage solutions has never been higher. One such innovation that has gained significant traction is custom plastic bulk containers with ramp walls. These containers are revolutionizing the way industries handle bulk materials, offering many benefits catering to various needs. In this blog post, we will explore the advantages of these containers, their applications, and why they are becoming the go-to choice for many businesses.
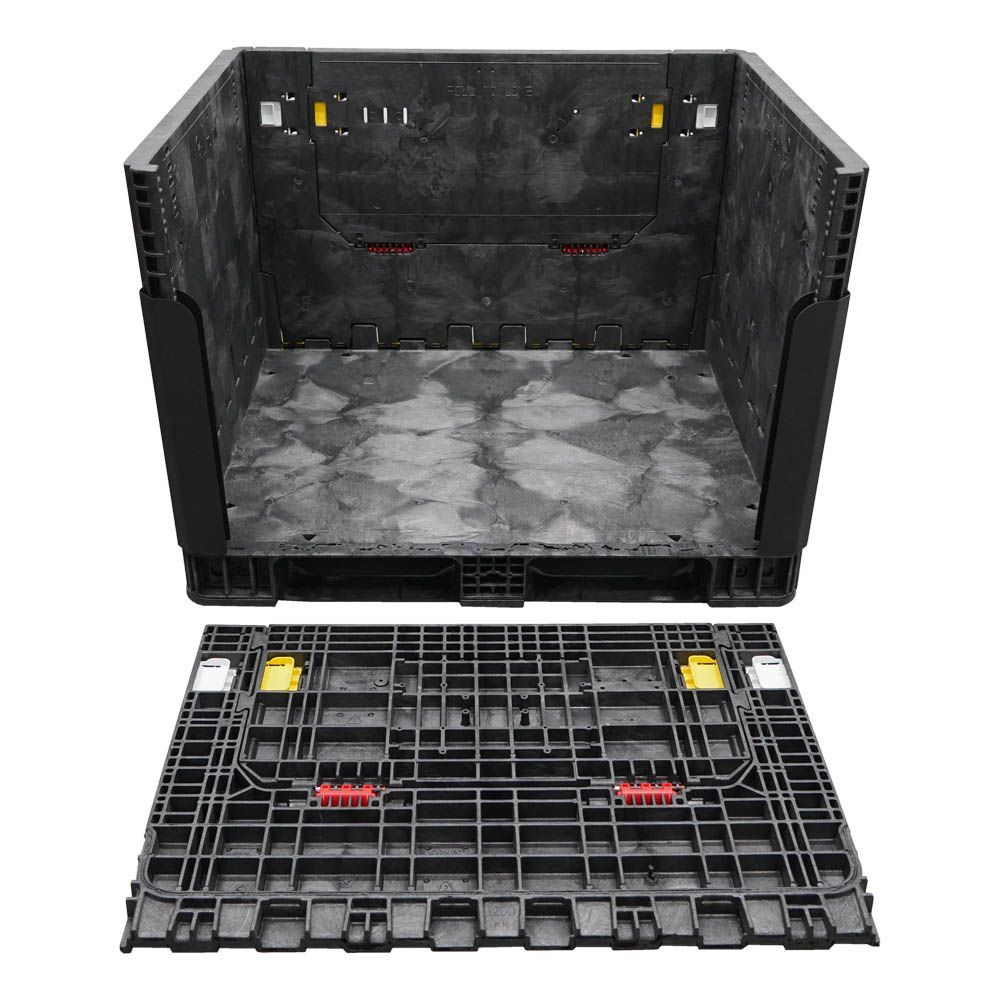
Bulk containers are an essential part of many industrial and commercial operations, providing a convenient and scalable solution for transporting and storing a wide variety of goods. However, as businesses evolve and adapt to changing needs, there often arises a necessity to modify the walls of these bulk containers to better suit their specific requirements. Whether it’s reinforcing the structure, adding access points, or enhancing insulation, wall modifications can significantly enhance the efficiency and functionality of bulk containers.
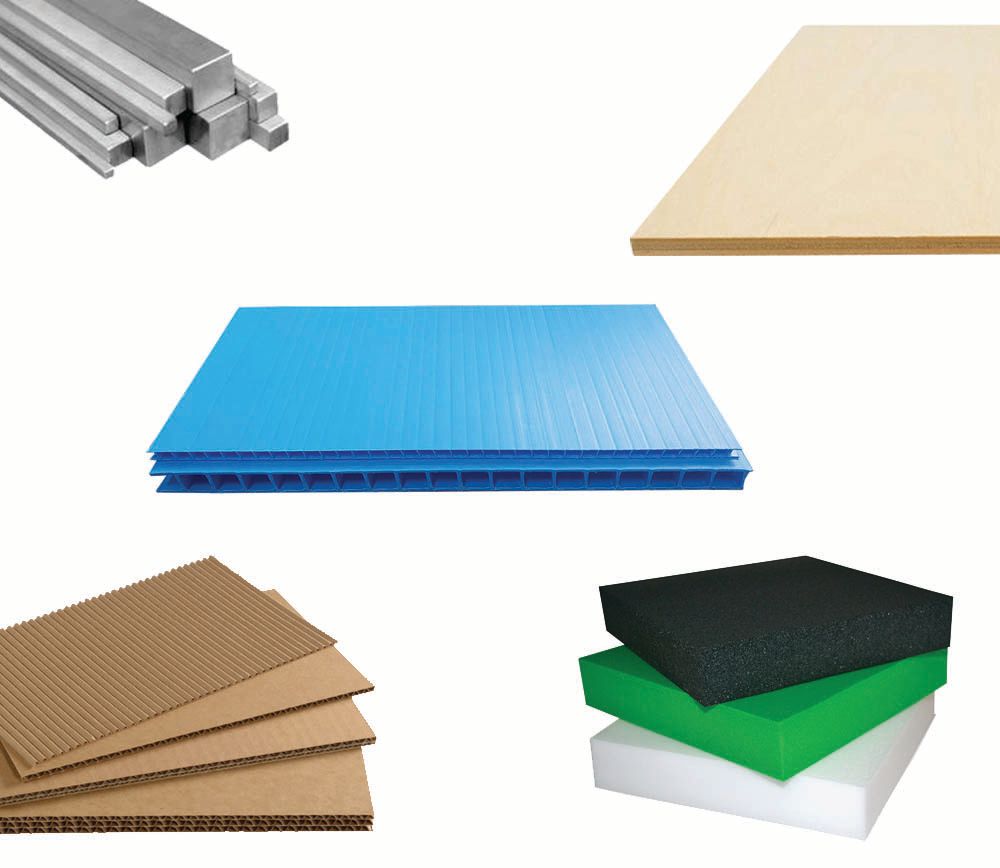
When shipping and storing goods in bulk containers, ensuring the safety and integrity of the products is of the utmost importance. This is where bulk container dunnage comes into play. Dunnage refers to materials used to support and secure cargo during transportation, and when it comes to bulk containers, the use of dunnage becomes even more crucial.
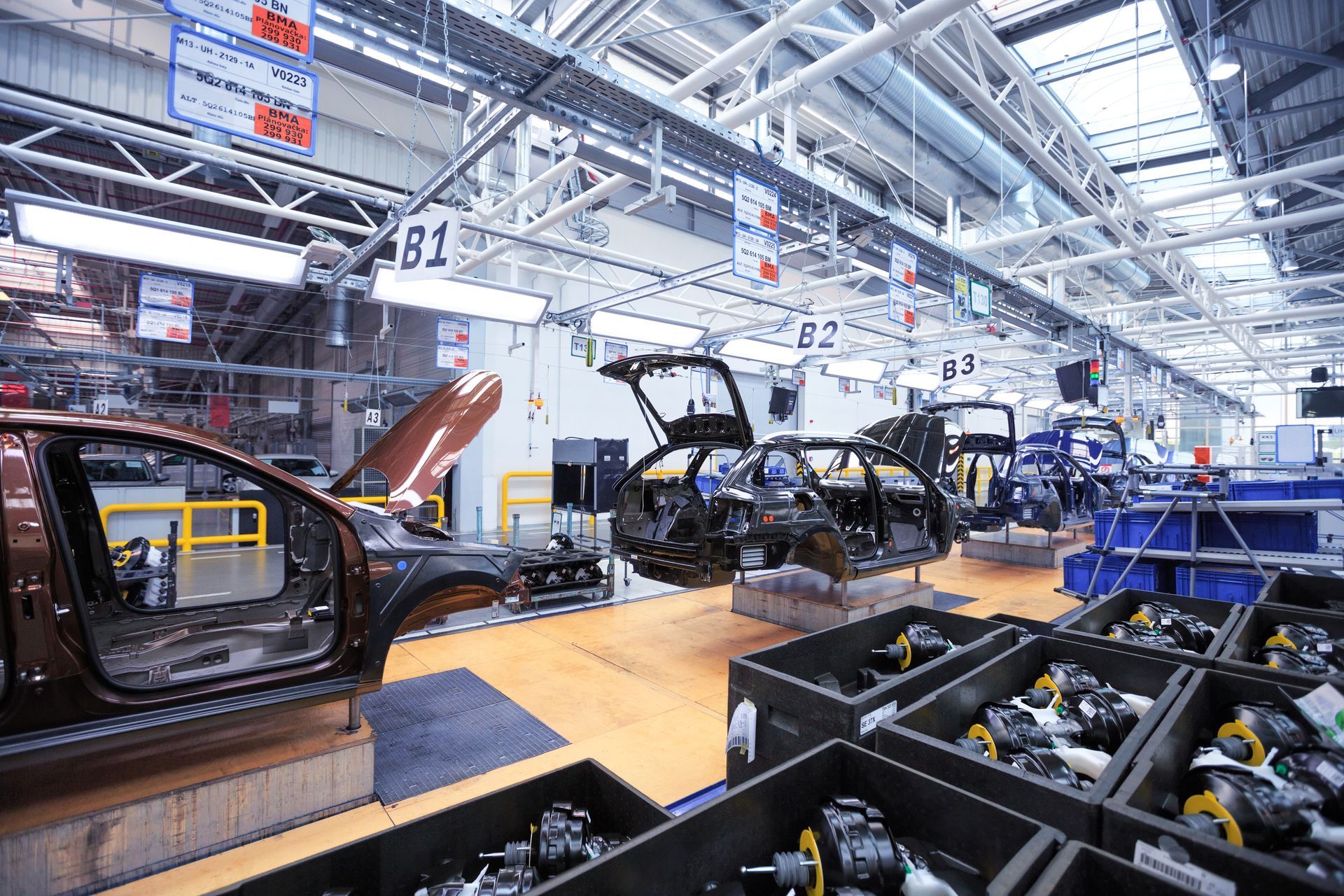
Returnable bulk containers, a sustainable choice, are extensively used in the automotive supply chain to transport and store various components and materials required in manufacturing. Their durable and reusable design makes them an economical option and a significant step towards reducing single-use packaging and promoting environmental responsibility.
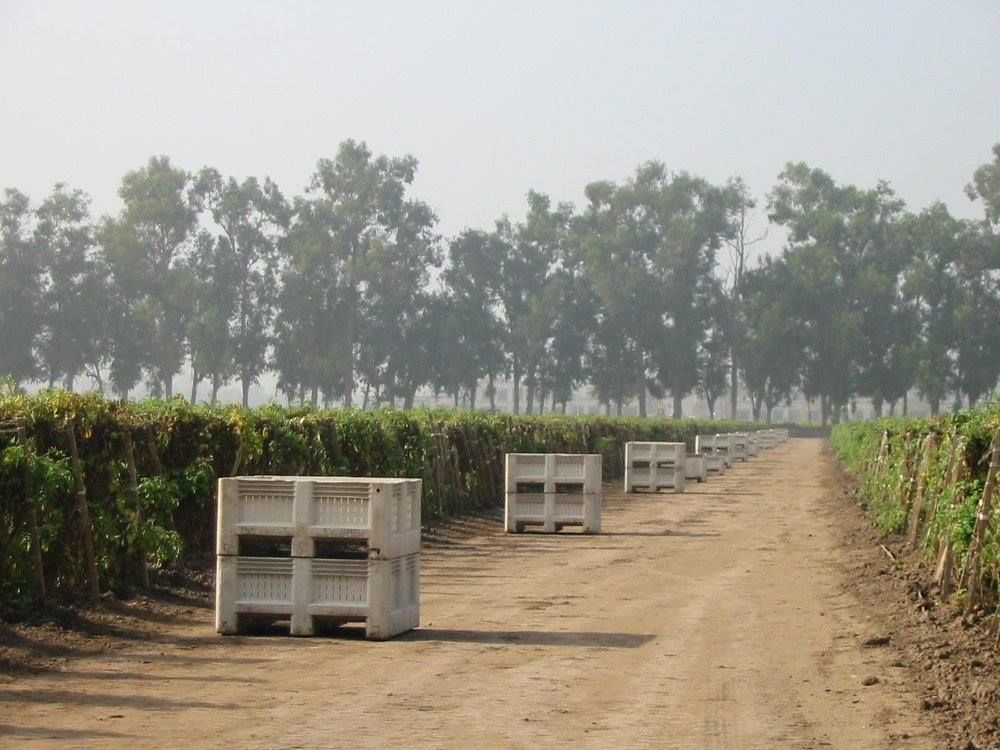
Agriculture, particularly fruit and vegetable growing and processing, is a very demanding business. It requires highly efficient, strong packaging and is resistant to harsh environments. RPP Containers has been at the forefront of meeting these needs. Our DuraGreen vented harvest bins and solid wall bulk bins protect produce, ensure quality, and preserve freshness from fields to supermarkets.
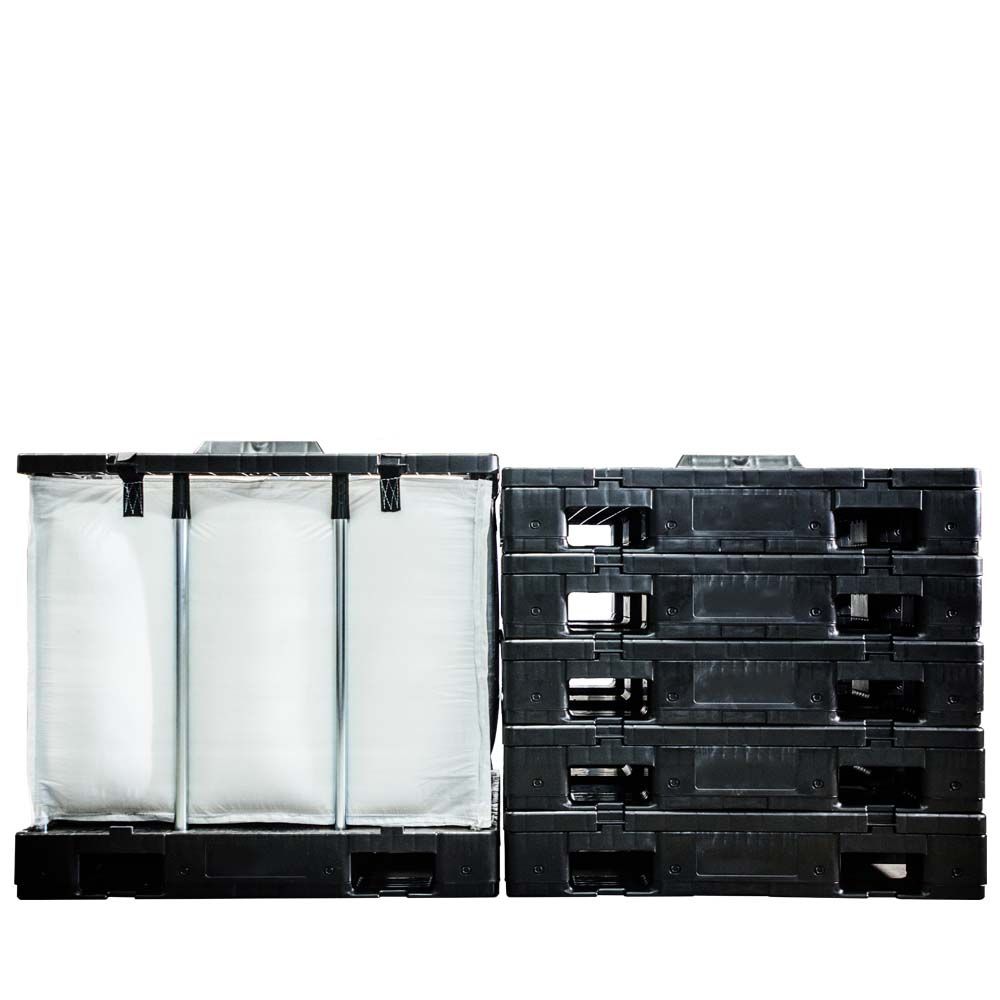
One game-changing innovation that has emerged in the industry is the 40 x 48 x 43 Stackable Foldable IBCs. These versatile containers offer a wide range of benefits that revolutionize the way goods are transported, stored, and handled. This article delves into the features and advantages of 40 x 48 x 43 Stackable Foldable IBCs, emphasizing their role in enhancing efficiency and promoting sustainability.